Rethinking UPS Maintenance: Why More Isn’t Always Better
- Continu Ups
- Mar 4
- 2 min read
Updated: Mar 10
For years, the standard approach to UPS maintenance has been simple—frequent preventative maintenance (PM) visits to keep systems in check. The logic seemed sound: the more often you inspect and service equipment, the more reliable it will be. Many IT Directors and Facilities Managers, have built their backup power strategy around this belief.
But what if this approach is actually increasing your risk, not reducing it?
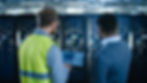
Many businesses stick to rigid PM schedules without questioning their actual effectiveness. Frequent on-site visits may disrupt environments, expose systems to unnecessary handling, and even increase failure rates.
Every battery test, every manual check, and every time a cover is removed, there’s potential for human error. Over time, this adds up—leading to more alarms, more emergency call-outs, and higher repair costs.
Instead of assuming that more maintenance is better, the smarter approach is targeted, data-driven decision-making. Of course there are widely recognised maintenance standards in the UK like SGG20, published by the Building Engineering Services Association (BESA) and used widely, particularly for by public sector.
Here’s how we do it:
Audit & Benchmark – We start by mapping out all UPS systems across a site or multi-site portfolio, establishing a clear view of what’s in place and its current health.
Assess Criticality – Not all UPS systems require the same level of maintenance. We categorize them based on their role, age, and the operational impact of downtime. Does SFG20 truly add value or should we tailor this with a data driven approach?
Apply the Right Strategy – Instead of blanket PM schedules, we tailor maintenance to fit the actual needs of the system. This includes proactive replacements, remote monitoring, and predictive analytics to prevent failures before they happen.
Reducing Call-Outs, Cutting Costs
A recent food production customer, managing backup power across multiple sites, faced too many emergency repairs and call outs despite a rigid PM schedule. Too many sub-contractors across various locations, added to the complexity. By shifting to a smarter maintenance model with efficient project management, installing remote monitoring and adjusting service schedules—we cut emergency call-outs by 40% and reduced overall maintenance costs by 30%.
The result? Fewer disruptions, better visibility, and lower costs.
What You Can Do Now
Evaluate Your Current UPS Strategy – Are you servicing equipment based on real data or just tradition?
Consider Remote Monitoring – Real-time insights eliminate guesswork and allow you to act before issues escalate.
Review Your Maintenance Contracts – Challenge whether your current service plan actually aligns with your business needs. Or perhaps there is no service plan?
Sometimes we hear "We need to follow the OEM recommendations."
however, the manufacturer guidelines set a baseline, but they don’t account for your specific site conditions, age of equipment, or actual usage patterns.
Sticking to outdated maintenance practices is costing your business money and increasing risk. Smarter, data-driven UPS management ensures continuous power while cutting unnecessary costs.
Let us take a fresh look at your backup power strategy—contact us for a site assessment.